Builders in hot-humid climates face two challenges: creating a resilient building envelope that keeps bulk water vapor out, and getting rid of moisture that inevitably finds a way in.
What makes the issue particularly complex is that some of the best strategies to keep water vapor from infiltrating into a building can also trap moisture inside.
Impermeable insulation prevents materials behind masonry or inside wall cavities from drying out as they should, leading to mold and mildew that can cause support structures to rot or swell and lead to less than desirable indoor air quality.
Semi-permeable insulation used as part of a moisture-control strategy reduces the transport of energy across air spaces and also promotes moisture exfiltration.
Masonry Walls and Vapor-Permeable Insulation
Water vapor moves from warm spaces to cold, necessitating different insulation strategies for different climates. The extremes of hot-humid climates call for permeable and semi-permeable air barrier membranes to minimize water vapor transmission (Builder’s Guide to Hot-Humid Climates, Lstiburek, 2010, page 118). In warm climates, vapor retarders (if used) are positioned as close to a building’s exterior as possible to prevent humid outside air from infiltrating into wall cavities and living envelopes.
Moisture, however, can still find a way to infiltrate. Water pipes can leak or break and heavy storms can damage a building enough to let water inside.
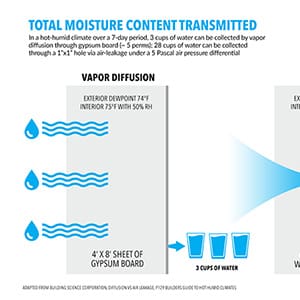
In such cases, a certain amount of vapor permeability is necessary to allow for interiors to dry. Vapor permeable insulation types that work well in hot-humid climates include:
- Fiberglass batt
- Unfaced fiberglass
- Cellulose
- Rock/mineral wool
- Perforated radiant insulation
These insulation options allow for the controlled movement of vapor out of interior cavities where moisture has managed to infiltrate.
The Evolution of Vapor Barriers/Retarders
In the past, builders understood that vapor transferred through air movement from areas of high pressure to low pressure. They were not as concerned with moisture migration through vapor diffusion.
Few contractors used vapor retarders, especially on materials like brick and concrete masonry that they believed were impermeable to moisture. Those who did calculated the amount of insulation manually using figures reflecting an average dew point for their region.
Over time, building science has discovered ways of reducing condensation, even on materials that were once thought to be impermeable. Computer simulators can now assist the specifier to make dew point calculations to figure in seasonal changes.
A number of online resources, including the U.S. Department of Energy’s Guide to Determining Climate Regions by County, can help home builders and contractors determine the materials and insulation strategies that work best for their climate zones.
Recent advances have led to the prolific use of vapor retarders on entire buildings to keep high pressure/high humidity air out of buildings (or keep it inside in cold climates). In hot climates with a lot of airborne water vapor, permeable and semi-permeable insulation and barrier types prove to be the most effective option to reduce the risk of moisture accumulation and mitigate damage within wall and ceiling cavities. Using permeable/semi-permeable insulation leads to more resilient buildings with better indoor air quality.
Dealing with Interior Air Pressure and Moisture
With air and vapor retarders essentially sealing the entire building envelope off from outside air, HVAC systems don’t have to work as hard to maintain indoor air temperatures and humidity levels. This strategy may provide an opportunity to offset some costs and living expenses by allowing for the installation of a smaller-load HVAC system.
Sometimes, however, this phenomenon leads contractors to install air conditioning units that are oversized. A correctly sized air conditioning system will help maintain ideal temperatures and humidity levels.
In systems that are too large, the coils don’t have enough time to pull moisture out of the air before the thermostat registers that the target indoor temperature has been reached, so the system shuts off prematurely. The shutoff results in higher humidity levels that can cause discomfort and moisture-related issues. It also can prompt owners to lower their thermostats, which increases energy usage and costs.
A unit that’s too small, on the other hand, won’t be able to handle the load to reach desired indoor air temperature. Specifiers should require that HVAC contractors utilize the American Society of Heating, Refrigerating and Air-Conditioning Engineers (ASHRAE) standards to understand the entire design, including insulation and vapor permeability of the building envelope, in order to select the right HVAC system to meet desired indoor air quality.
Fi-Foil and Masonry VR Plus Shield™
Fi-Foil Company’s VR Plus Shield™ is specifically designed to help control water vapor in masonry construction. This three-layer radiant insulation adds R-7.0 with a minimum 1½” enclosed cavity air space. Notably, it also reduces radiant heat transfer for more efficient, comfortable buildings. VR Plus Shield™ is available in a semi-permeable version with perforations to allow water vapor out in hot-humid zones for better indoor air quality and building resiliency.
Find out more:
Building Science Corp.: Builder’s Guide to Hot-Humid Climates
U.S. Department of Energy: Guide to Determining Climate Regions by County
American Society of Heating, Refrigerating and Air-Conditioning Engineers: ASHRAE.org